AP Sensing: above-ground conveyor belt monitoring
- July 23, 2020
- 9:15 am
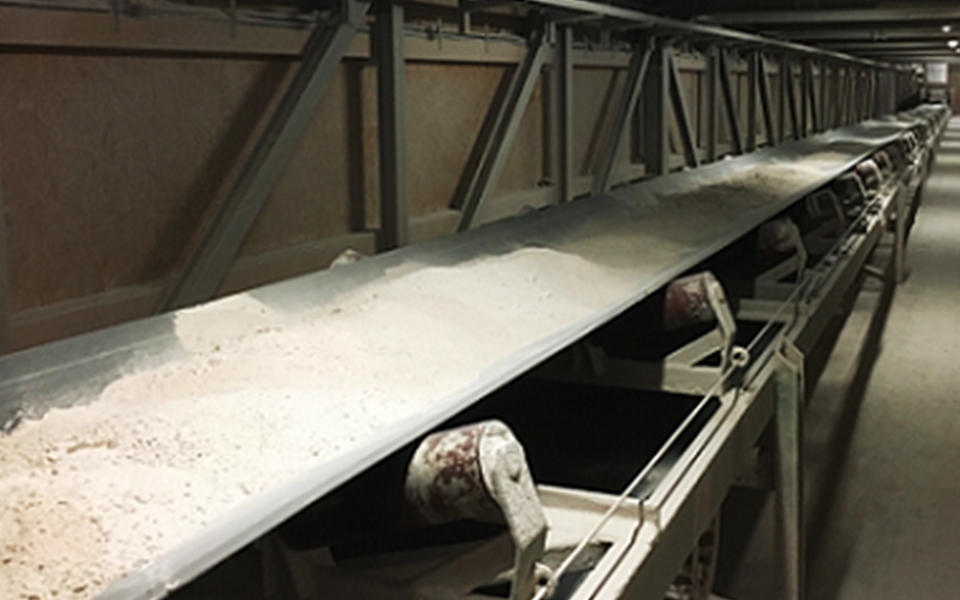
Matt Head
Share this content
AP Sensing is monitoring conveyor belts at the largest salt production site in Germany. The Zielitz Plant extracts approximately 12 million tons of crude salts per year and the mine operator, K+S, is an international mining company with sites across five continents.
K+S pursued an AP Sensing fire detection solution for early detection on conveyor belt bridges. Such bridges typically have a wooden floor, which would burn quickly. AP Sensing’s Linear Heat Detection (LHD) protects these conveyor belt bridges, and due to the project’s success and AP Sensing’s scope of certifications, K+S and AP Sensing entered a firm partnership to equip further sites.
In total, 22 conveyor belts are monitored with 11 LHD devices spread across the entire site. The operator, K+S, conducted trials and a benchmark comparison at the beginning of the project, additionally testing thermo cameras and point sensors. But due to the salty air in the conveyor belt bridges, the other sensor types were unsatisfactory as the corrosion of components is high, visibility low, and the maintenance effort higher.
AP Sensing’s simple approach, combining our sensor cable along the conveyor and LHD units in different control rooms, is the best solution for this type of application and its tough environmental conditions.
Conveyor Belt Monitoring
The conveyor belts are used to transport the salt from the ground to the storage halls, mills, other production facilities and load out ramps. After an incident at another site where one conveyor belt bridge burned, K+S sought out a fire detection system. These conveyor belts are important to monitor as none of them are redundant.
Installation
Following a successful pilot installation, K+S installed 11 fibre optic LHD units. All units have two channels and work in a fully redundant setup. AP Sensing’s Sensor Cable Steel is installed along both sides of each conveyor to achieve maximum coverage and the fastest possible detection. The cable has been fixed with high temperature cable ties along a tension wire.
Fire Coverage
To guarantee quality and reliability in the harsh conditions of the mine, a robust and maintenance free fire detection system is necessary. This solution consists of over 10 km of cable distributed throughout the site, providing area coverage for the conveyors, three reclaim tunnels, the handling and preparation plant, and the train load out conveyor and bin.
Precision of detection is unaffected by wind, dust and harsh environmental effects. All LHD units transmit alarms via relay contacts to different alarm panels on site in order to inform the plant fire brigade immediately. Additionally, AP Sensing’s SmartVision™ asset visualisation software is in use to demonstrate the exact location of temperature events along the conveyors.
The project was successful and K+S used AP Sensing’s LHD solution for other K+S sites. AP Sensing’s DTS technology is ideal for the extreme environmental conditions often found in mines. It is fully certified, resilient and maintenance-free, withstanding extreme temperatures without losing monitoring capabilities. Fibre optic LHD provides a simple and cost-effective solution for minimising serious damage, protecting employees and reducing operational shutdowns.