Smoke Control Association calls for compliance in smoke control systems in UK buildings
- June 25, 2024
- 10:22 am
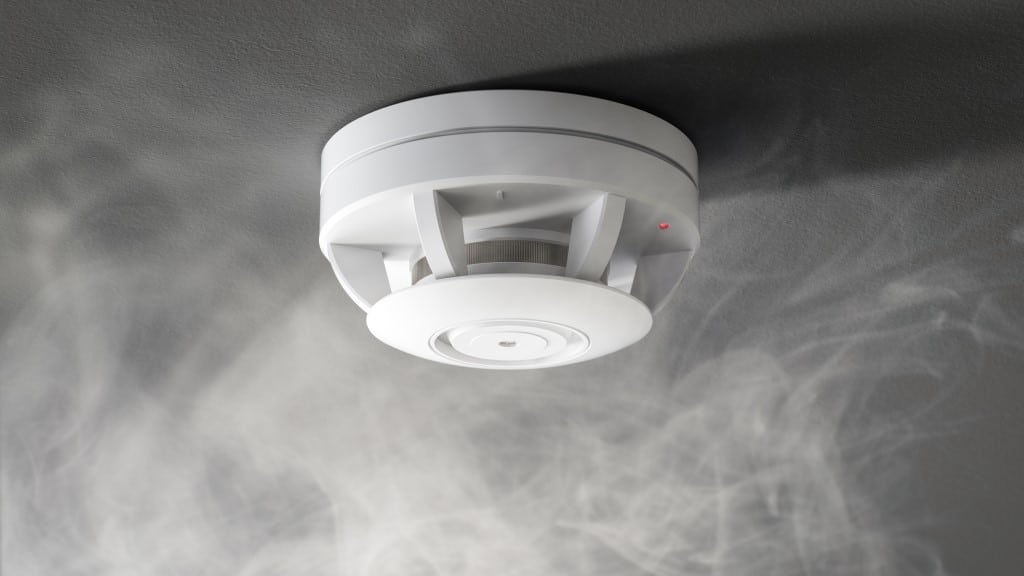
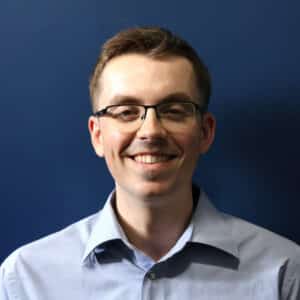
Iain Hoey
Share this content
Compliance with EN12101 standards
According to the Smoke Control Association, smoke control systems are vital in ensuring safety in buildings during fire emergencies.
These systems maintain smoke-free escape routes and facilitate fire-fighting operations.
Since the Construction Products Regulations (CPR) were introduced in 2013, all smoke ventilation products and systems used in the UK must conform to the EN12101 standards.
Non-compliant products cannot receive the CE or UKCA marks, which are essential for legitimacy.
The association points out that EN12101-2, a key standard within the suite, applies to natural smoke and heat exhaust ventilators (NSHEV).
These systems maintain a smoke-free layer by removing smoke and hot gases during a fire.
The standard requires that the vent and actuator are tested together at an accredited facility to ensure reliable operation during emergencies.
Compliance is certified through a stringent process, verifying that products meet the necessary specifications.
The role of the SDI 19 certification scheme
The CPR has led to advancements in ensuring the use of compliant products in smoke control systems, bolstered by the IFC Certification SDI 19 scheme.
This scheme ensures competency in fire strategy verification, system design, installation, and commissioning of smoke control systems.
As the association explains, the scheme is mandatory for Smoke Control Association members involved in the installation of smoke ventilation systems.
The SDI 19 installer scheme has various classifications:
- Category 1: Companies that perform small refurbishments, remedials, and replacement projects, and install EN12101 compliant products and controls.
- Category 2: Companies installing code-compliant staircase AOV systems, corridor smoke ventilation systems, and simple natural smoke ventilation systems without significant design input.
- Category 3: Companies installing natural smoke shafts, smoke damper installations, and natural smoke ventilation for various building types.
- Category 4: Companies installing complex smoke control systems, including mechanical smoke shafts, pressurisation systems, and car park smoke control systems.
Ongoing challenges and the importance of compliance
The Smoke Control Association notes that while the CPR and SDI 19 installer scheme have brought positive changes, there are still areas requiring improvement.
Individual nations and regions must emphasize that standards apply throughout the UK.
Proof of compliance in the form of a Declaration of Performance (DoP) is essential to ensure that any life safety product or system is fully compliant with UK law.
The DoP can be requested by clients, contractors, or approved inspectors.
Reputable manufacturers should provide a DoP to prove independent testing and certification.
Products lacking a valid DoP are not compliant and should not be on the market.
A full audit of the supply chain by a third party adds confidence that all elements comply with relevant laws and industry standards.
Following the Grenfell Tower fire, Dame Judith Hackitt’s Independent Review of Building Regulations and Fire Safety recommended clearer, more transparent, and more effective product specification and testing regimes.
The Smoke Control Association stresses the need for organisations across the country to understand their safety obligations when bringing life-critical products to market.
Non-compliance may be monitored by Approved Inspectors, Building Control Officers, and the Office of Product Safety Standards, but overall responsibility lies with the company bringing the product to market.